I started the AJAK sensor mod in this thread http://www.satelliteguys.us/xen/threads/10-cm-perf-on-ajak-h180.311276/
The design of the current revision is based on the original design. All magnets polarized the same way N or S and a reed switch that is placed so it counts each passing magnet twice. The stock sensor was 5 magnets for 10 counts per revolution. I use 10 magnets for 20 counts. The wheel pictured below.
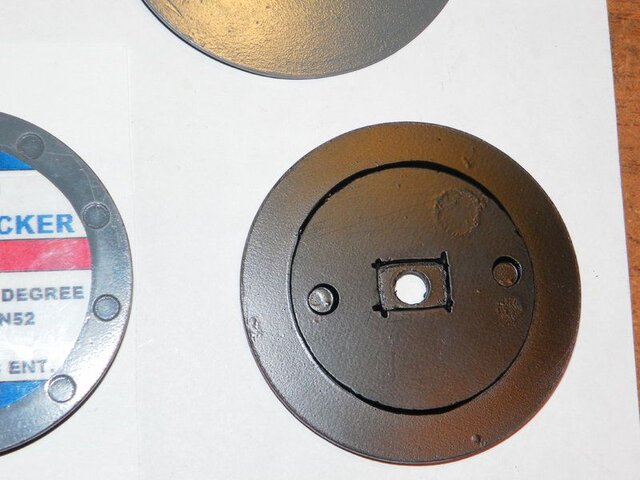
There are two switch and cover plate assemblies that I am working with. One uses a molded body reed switch and the other is a glass tube like the original.
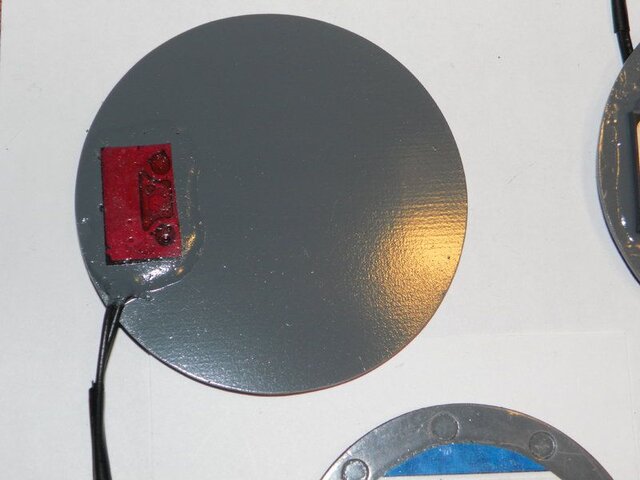
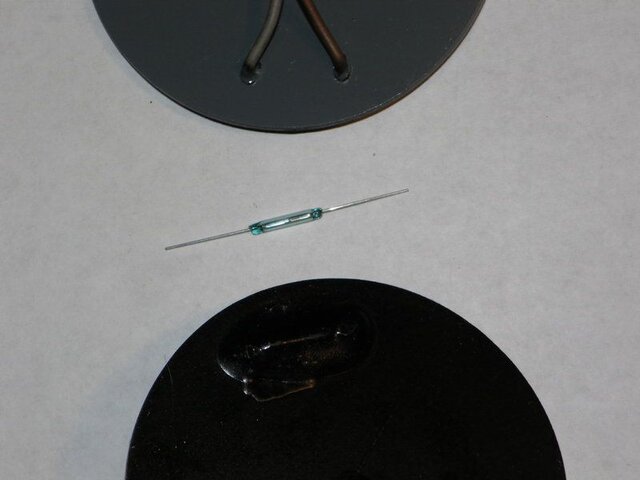
After rewiring the AJAK with ribbon cable it looked like this.
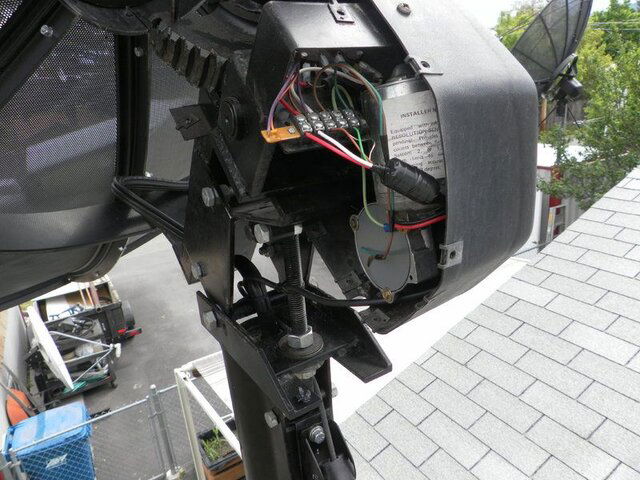
Because the sensor wiring is so close to the motor can it didn't work with any controller at this point.
I moved the wiring in the terminal block to move the sensor wiring away from the motor. It helped but wasn't perfect.
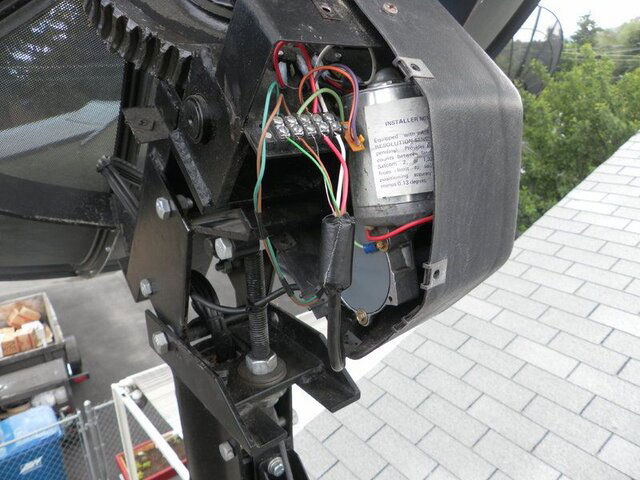
I decided to try and remove as much of the sensor wiring as possible to further remove it from influences from the motor. I also added a capacitor to eliminate switch bounce type signals. But the latest firmware had already saw to that issue.
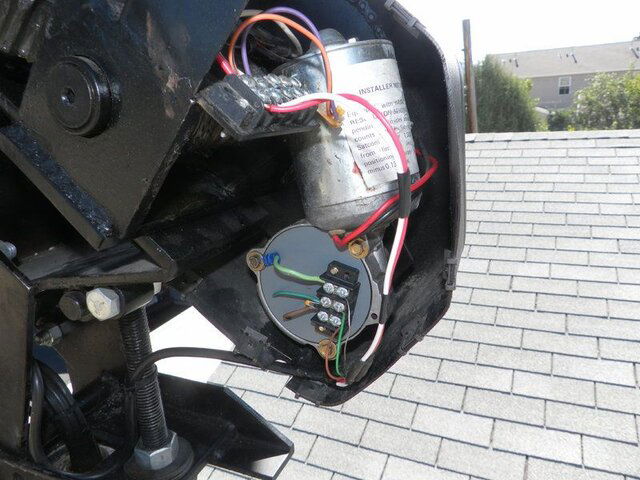
This is where I am at today. The VBox likes this and the ASC1 doesn't
I would really like to know if it worked with a stock sensor, but I don't have one.
The design of the current revision is based on the original design. All magnets polarized the same way N or S and a reed switch that is placed so it counts each passing magnet twice. The stock sensor was 5 magnets for 10 counts per revolution. I use 10 magnets for 20 counts. The wheel pictured below.
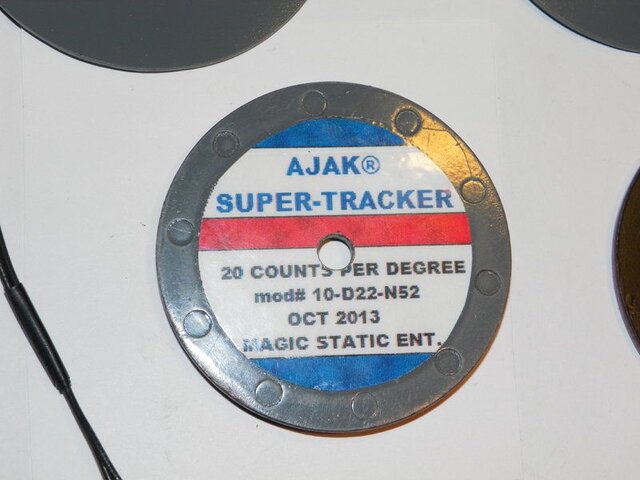
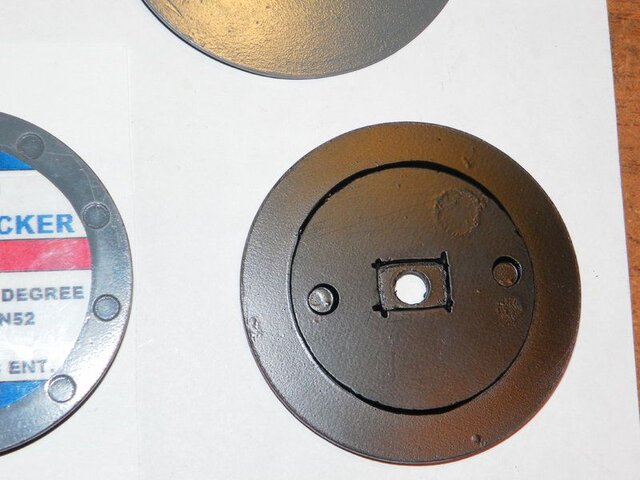
There are two switch and cover plate assemblies that I am working with. One uses a molded body reed switch and the other is a glass tube like the original.
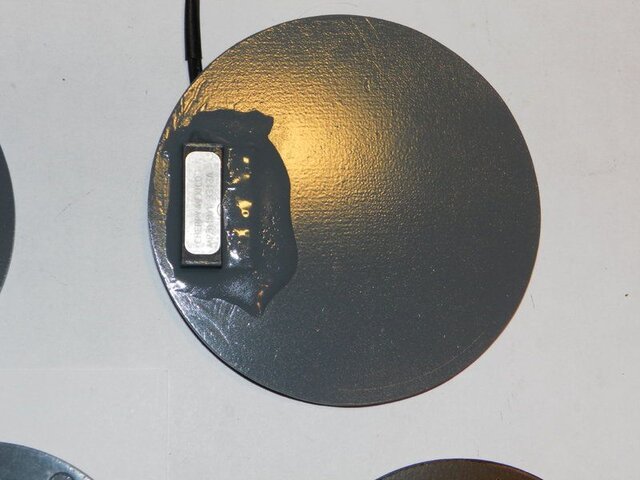
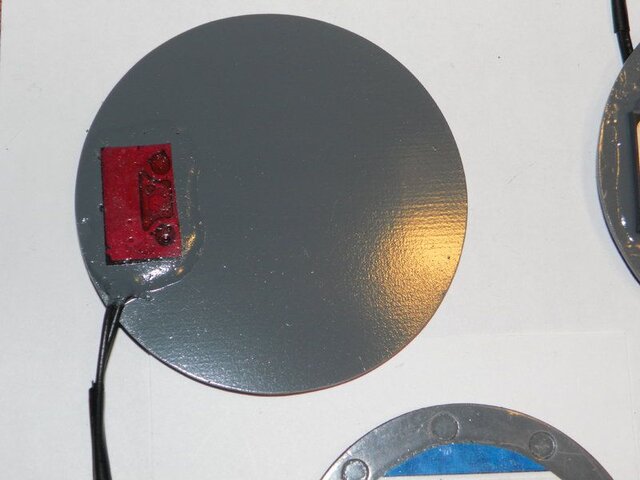
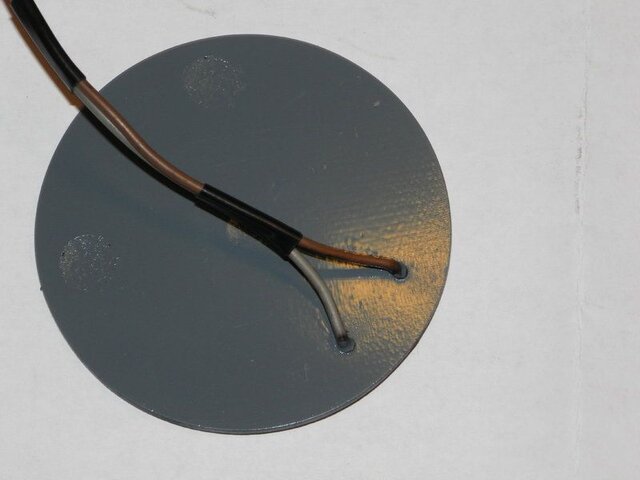
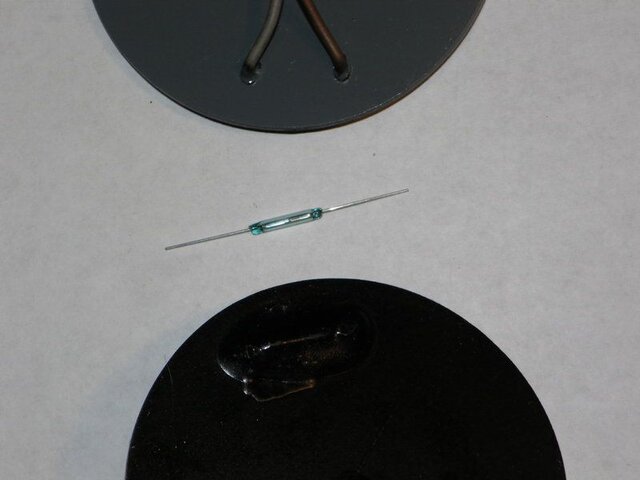
After rewiring the AJAK with ribbon cable it looked like this.
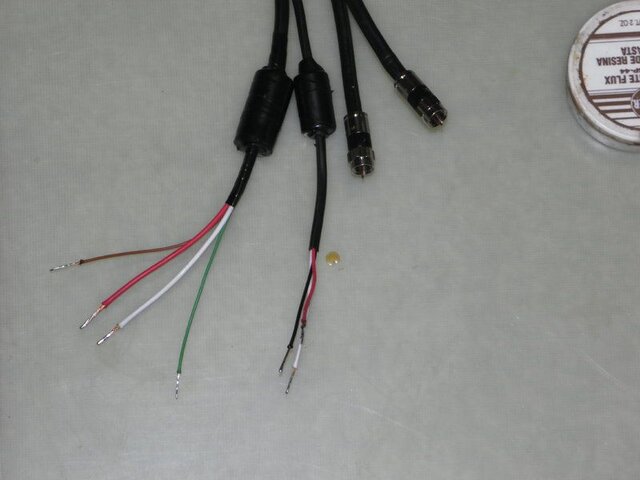
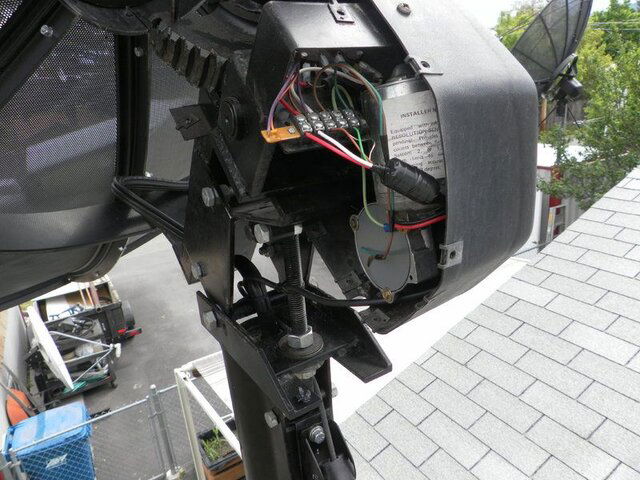
Because the sensor wiring is so close to the motor can it didn't work with any controller at this point.
I moved the wiring in the terminal block to move the sensor wiring away from the motor. It helped but wasn't perfect.
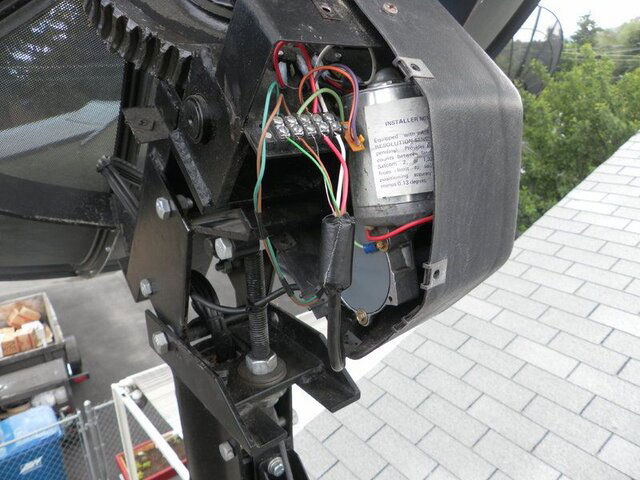
I decided to try and remove as much of the sensor wiring as possible to further remove it from influences from the motor. I also added a capacitor to eliminate switch bounce type signals. But the latest firmware had already saw to that issue.
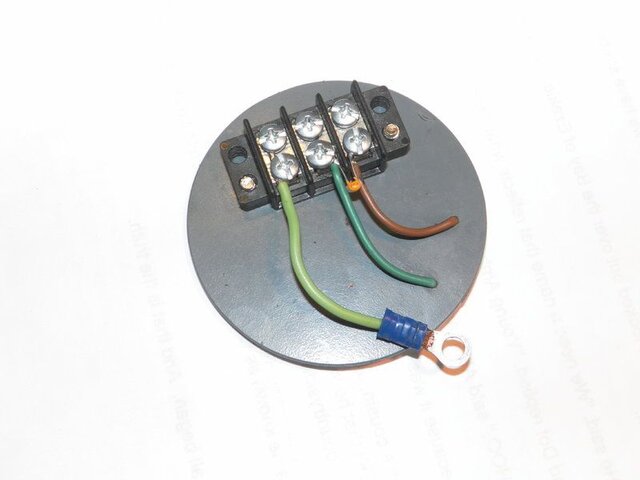
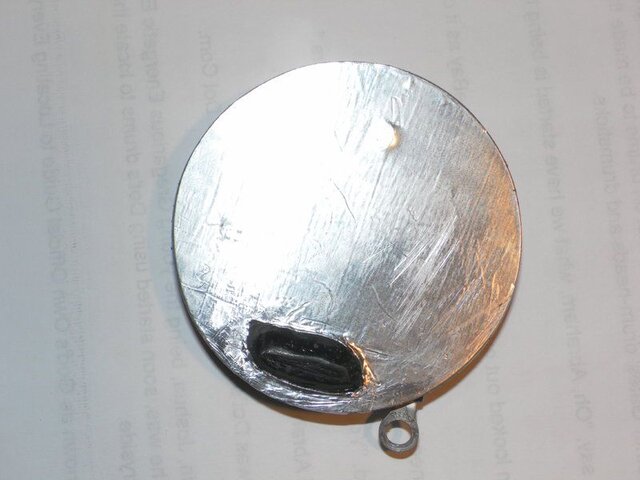
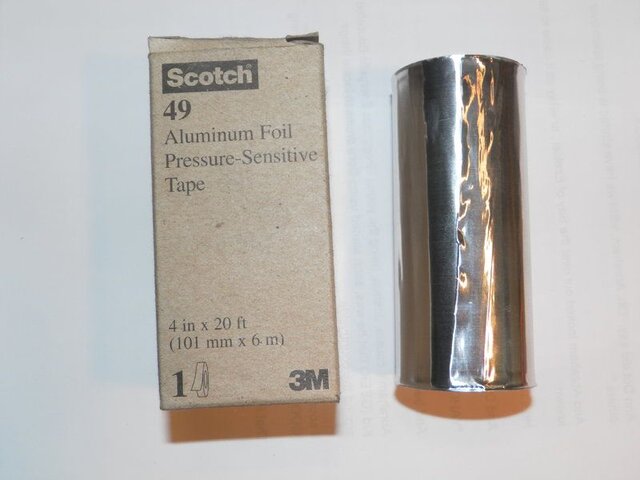
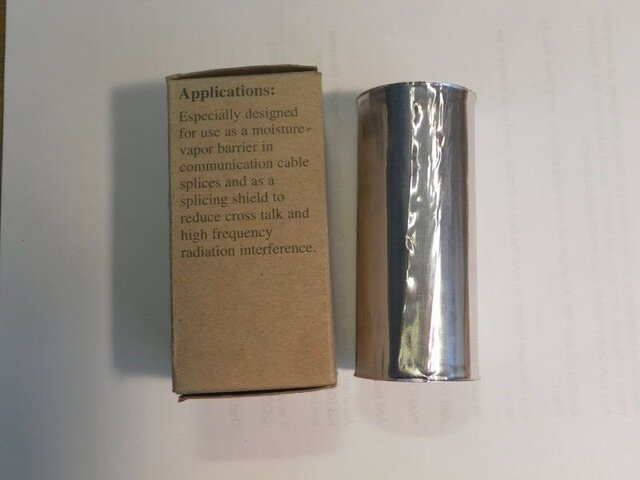
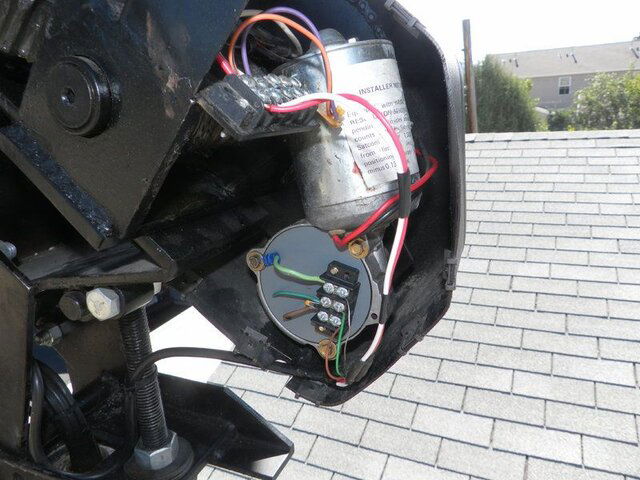
This is where I am at today. The VBox likes this and the ASC1 doesn't

I would really like to know if it worked with a stock sensor, but I don't have one.